Le MES est-il compatible avec le Lean Manufacturing ?
Est-ce que le MES est compatible avec le Lean Manufacturing ?
A écouter les puristes du Lean, on finirait par croire que les principes du Lean Manufacturing sont à l’opposé de ceux du MES. Le MES serait un obstacle pour implémenter le Just-In-Time et pour rendre chaque collaborateur acteur de l’amélioration continue. Faut-il croire qu’un peu de technologie utilisée à bon escient ne pourrait pas au contraire accélérer la mise en œuvre du Lean Manufacturing ?
Prenons l’exemple de plusieurs outils du Lean Manufacturing :
- La méthode 5S : cette méthodologie vise à mettre de l’ordre, standardiser et maintenir dans le temps. Or une application peut justement apporter la rigueur nécessaire (contrôle, rappels périodiques, procédure d’exécution) bien plus qu’un processus papier. Plutôt que coller des photos sur un tableau blanc, pourquoi ne pas directement prendre et visualiser les phots avant / après. Mieux qu’un formulaire, pourquoi ne pas procéder aux contrôles via une check-list numérique liée à une base de donnée (pas de ressaisie) et dotée de règles qui seront appliquées ?
- Andon : c’est le management visuel par excellence, utiliser notamment pour connaitre l’état réel des équipements et des opérations. Le temps réel est seulement possible avec une solution digitale et connectée. Plutôt que d’installer ces gyrophares assez disgracieux et encombrant, pourquoi ne pas appliquer ce principe en affichant les états machines sur une smartTV placée à un endroit clé de l’atelier ? c’est plus facile d’interagir avec l’écran pour connaitre la nature d’une panne par exemple. C’est aussi plus pratique quand le parc machine est très vaste.
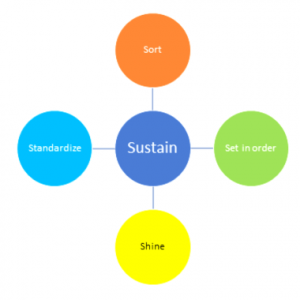
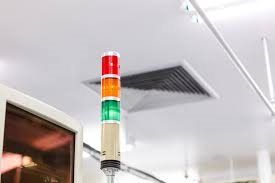
- Flux continu : avoir le minimum d’en-cours entre les postes de travail en synchronisant les priorités tout au long de la chaine de production. Ce n’est possible qu’en ayant la vue globale sur l’ensemble des ateliers et un algorithme de priorisation performant, et donc pas gérable manuellement. Les méthodes d’équilibrage des flux requièrent une connaissance en temps réel des en-cours et des priorités, ce qui n’est pas possible avec des outils manuels ou bien excel.
On pourrait aussi trouver des avantages à digitaliser le Kanban, le Heijunka ou le Poka-yoke. Le MES doit s’adapter à vos besoins et non l’inverse. C’est dans cet esprit que le MES SMARTPROD a été conçu : flexible, centré sur l’utilisateur et simple à utiliser.
Si ces sujets vous concernent, n’hésiter pas à échanger vos idées avec nous et nous trouveront ensemble les solutions techniques qui apportent une vraie valeur ajoutée à votre démarche Lean Manufacturing.