Des pistes pour vaincre la peur du changement – Partie 2
Réussir son projet de digitalisation
Comment changer l'état d'esprit ?
Partie 2 : Des pistes pour vaincre la peur du changement
Le discours incantatoire est contre-productif : dire à quelqu’un d’arrêter d’avoir peur ne fonctionnera tout simplement pas, car la peur ne peut pas simplement être désactivée. Pour vous en convaincre, emmenez des amis sur une via ferrata pour la première fois de leur vie et vous aurez vite compris ce qui suit : la peur est une émotion, et ne se contre pas avec un argument rationnel. Pour aider quelqu’un à surmonter sa peur, vous devez chercher ce qui le motiverait à faire le saut dans l’inconnu. Quel est l’avantage ou la récompense nécessaire pour que cette personne dépasse sa peur ?
Nous acceptons le changement si nous en percevons le besoin, ou si nous y trouvons un vrai avantage (nos attentes sont mieux satisfaites) et parfois nous subissons le changement lorsque nous y sommes contraints (question de survie, contrainte légale) et dans ce cas, on essaiera de contourner ou de faire une obstruction passive. Pour convaincre et non contraindre, vous devez faire en sorte que la récompense soit plus grande que la peur.

Quelques moyens pratiques d’augmenter la récompense :
- Si l’innovation est un objectif clé pour votre entreprise, alors les objectifs liés à la rémunération variable ainsi que les critères d’embauche et de promotion doivent valoriser cette prise de risque et cet esprit d’innovation
- Personnaliser l’avantage en répondant à la question « qu’est-ce que j’y gagne ? » : chaque cas est individuel, mais ilexiste des avantages qui touchent le groupe comme la valorisation de ces nouvelles expériences dans le monde du travail de demain, les chances de promotion interne et l’impact sur l’image globale de l’entreprise. Il faut aussi rassurer ceux qui craignent pour la pérennité de leur emploi quand les tâches les plus répétitives seront « automatisées » en les accompagnant vers des fonctions à plus forte valeur ajoutée par de la formation interne, car la digitalisation créée aussi de nouveaux besoins (plus de données disponibles à exploiter) et de nouveaux métiers (tâches non répétitives demandant de la créativité et/ou de l’expérience, que la concurrence ne peut pas offrir).
- Chiffrer le coût et l’impact de cette non-prise de risque : se poser honnêtement la question « qu’est-ce que l’on risque à ne rien faire ? » implique de regarder ce que fait la concurrence et de connaitre l’évolution des attentes du marché. Se lancer trop tard coute plus cher que se lancer trop tôt car la place est déjà prise et les talents sont déjà chez la concurrence.
- Adopter un mode de management qui « implique » les collaborateurs et encourage leur esprit d’initiative (les échecs sont des occasions d’apprendre et non plus des raisons de blâmer). Il faut féliciter les « pionniers » qui œuvrent pour apporter des changements qui vont apporter de nouveaux avantages concurrentiels (indépendamment du résultat à court terme). Écouter et répondre aux questions des collaborateurs. Solliciter les plus réfractaires aux changements en demandant leur avis sur la façon d’améliorer les choses, ils proposent souvent d’excellentes idées et se rallieront plus facilement au changement.
- Citer des exemples d’entreprises qui se sont concentrées sur ce qu’elles ont bien fait et qui ont raté le virage technologique suivant (Kodak, Olivetti, BlackBerry, les exemples ne manquent pas…). Donner surtout des exemples internes lorsque des clients ont été perdus au profit de concurrents plus innovants, mais aussi des exemples où des progrès ont été réalisés en apportant quelque chose de nouveau.
En résumé, comprendre la peur naturelle et y répondre par des incitations plutôt que par des incantations, est la meilleure façon de développer la capacité d’innovation de votre organisation. Sachez faire confiance à des solutions nouvelles, même sans référence, si vous pouvez les expérimenter par vous-même et qu’elles répondent à votre propre stratégie d’entreprise. Qui aurait misé sur SAP en 1971, sur Tesla en 2003 et sur Amazon Web Services en 2006 ?
A votre écoute
Partagez avec nous vos idées sur la mise en pratique de l’industrie 4.0 dans votre entreprise.
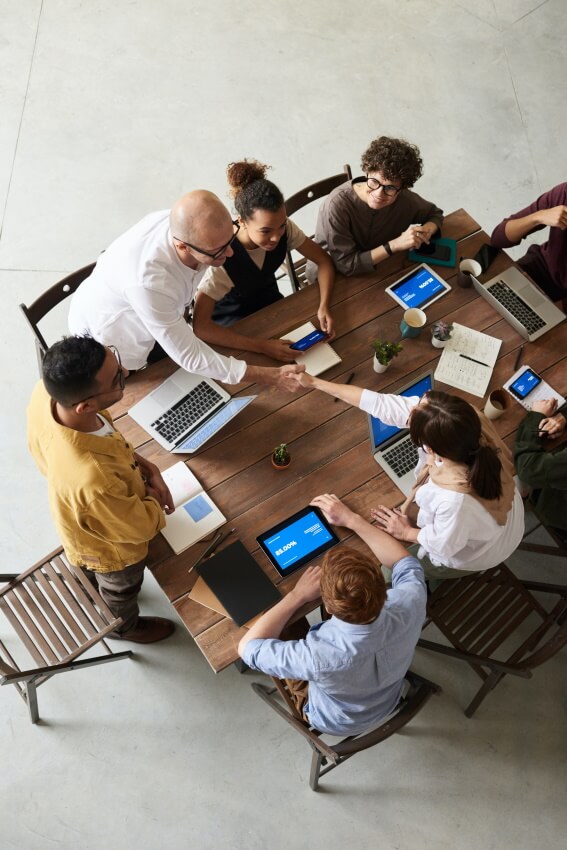