Features
Simplicity
Our application is easy to use to facilitate adoption by all users in the company.
Connectivity
SMARTPROD is connected to machines (150 OPC-UA or not, open to other applications (ERP, HR…) in order to share information in complete security.
Mobility
Our solution is mobile, usable on smartphone, tablet, PC and Smart TV and can work in offline mode.
Functional areas
Shop floormanagement
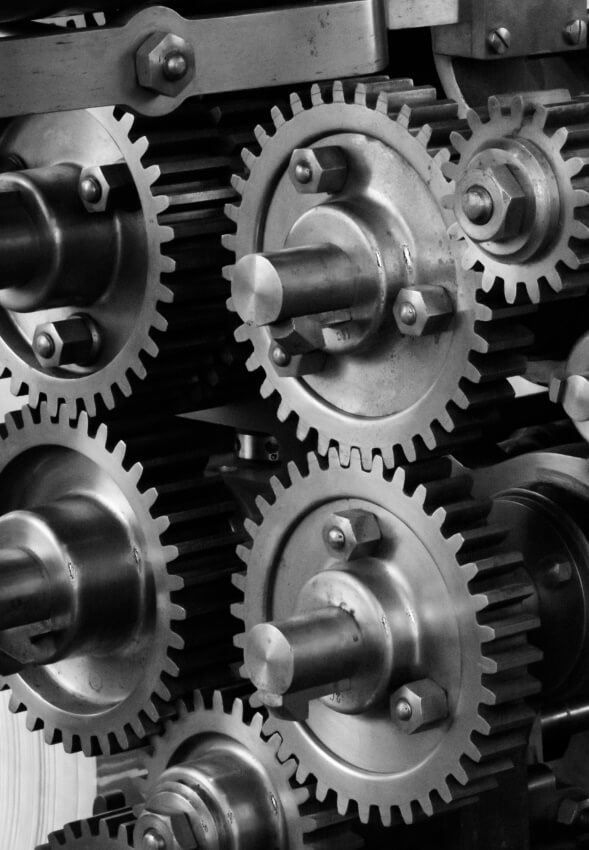
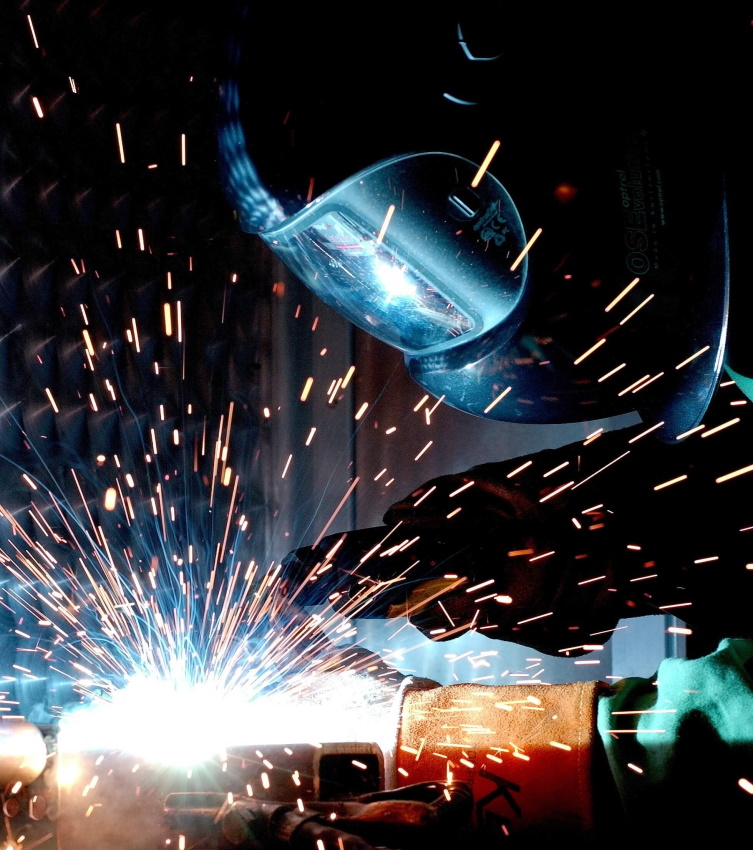
Work-in-process management
Collaborative management
In the event of a production shutdown, alerts are sent to members of the production support teams. The process of handling alerts is managed from start to finish in the application to provide greater responsiveness and transparency between departments
The Methods department will also be able to use the application to plan its work preparation actions. It will also use the actual data to improve the accuracy of standard times or review operating procedures. It can create inspection plans that allow operators to enter quantitative and qualitative controls and the tools used.
The Quality department will be involved in the management of the batches to be reworked. After analysis, the choice of the rework operation will be confirmed in the application by the quality engineer. The scrap, rework and rework success rates can be more finely analyzed with the data collected by the application than with the ERP.
Between shop floor managers, short-term scheduling can also be more collaborative because the status of work in progress is visible to all workshop managers. By managing the order of operations, each workshop is synchronized with the others to produce the parts expected by the market.
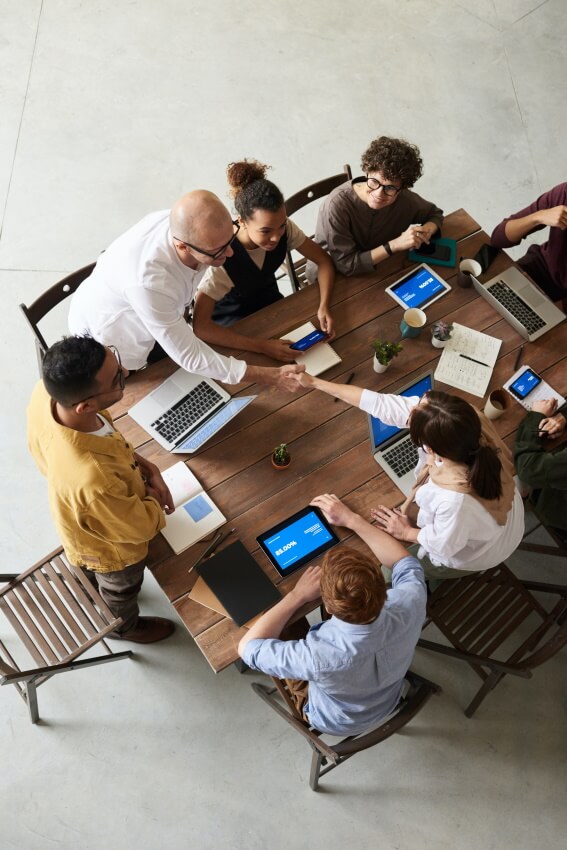
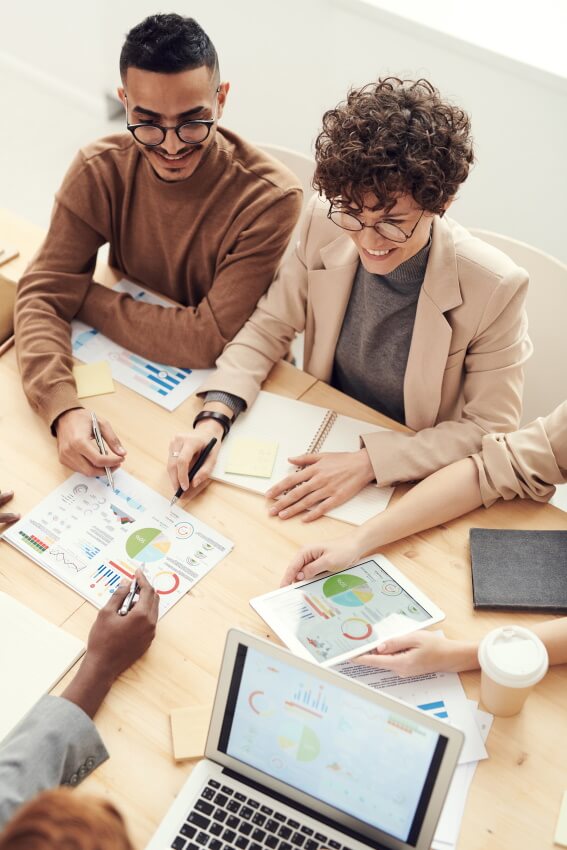
Team Leadership
The team leader can allocate critical operations to machines and operations taking into account priorities, his team’s skill matrix and current work in progress. This fine-tuned planning of individual resources takes into account the actual available capacity of each resource (absence, maintenance, shift schedules, etc.).
The reporting tasks of shop floor managers are greatly reduced by the availability of ready-to-use indicators. Team meetings are facilitated by the relevance of these indicators, allowing immediate actions to be identified more quickly.